Advertisement
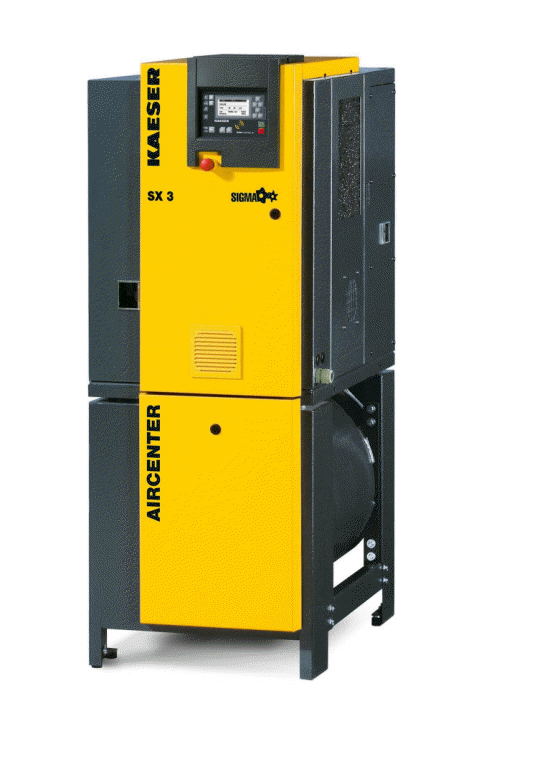
Nowadays, most dental laboratories want a complete in-house CAD/CAM system for in-lab milling. However, successful integration of a milling centre often requires evaluation and, in many cases, upgrading of the compressed air supply. Enter the KAESER Aircenter, the ideal solution to meet these evolving needs.
The vast majority of CAD/CAM systems now rely on compressed air. Installation of a milling centre typically increases both compressed air demand and, most importantly, required pressure. A minimum pressure of 7 bar is now commonly needed to ensure secure clamping of tools, smooth tool changes, effective work area cleaning, and proper cooling of workpieces. These factors are essential for producing flawless results, such as high-quality frameworks for bridges or crowns. Whilst the air quality of an existing compressed air supply system can be enhanced with dryers and filters, the pressure cannot. If a compressor is not factory-designed to deliver the required pressure, no additional adjustments can be made later on. Furthermore, unauthorised modifications not only void the manufacturer’s warranty, but also lead to increased machine wear and potential safety risks.
In a dental laboratory, the goal is to run the milling machine at full capacity, ideally 24/7, including weekends. Therefore, high-demand environments such as these preclude extended periods of compressor downtime, and in digitised laboratories, where compressors often run ten times more than those in conventional labs, energy efficiency is paramount. Rest assured then that the Aircenter’s rotary screw compressor design handles the workload effortlessly and with exceptional efficiency. Renowned for its low energy consumption and minimal CO₂ footprint, the KAESER Aircenter not only supports sustainability goals but also delivers reliable, round-the-clock performance tailored to meet the needs of modern dental laboratories.
The vast majority of CAD/CAM systems now rely on compressed air. Installation of a milling centre typically increases both compressed air demand and, most importantly, required pressure. A minimum pressure of 7 bar is now commonly needed to ensure secure clamping of tools, smooth tool changes, effective work area cleaning, and proper cooling of workpieces. These factors are essential for producing flawless results, such as high-quality frameworks for bridges or crowns. Whilst the air quality of an existing compressed air supply system can be enhanced with dryers and filters, the pressure cannot. If a compressor is not factory-designed to deliver the required pressure, no additional adjustments can be made later on. Furthermore, unauthorised modifications not only void the manufacturer’s warranty, but also lead to increased machine wear and potential safety risks.
In a dental laboratory, the goal is to run the milling machine at full capacity, ideally 24/7, including weekends. Therefore, high-demand environments such as these preclude extended periods of compressor downtime, and in digitised laboratories, where compressors often run ten times more than those in conventional labs, energy efficiency is paramount. Rest assured then that the Aircenter’s rotary screw compressor design handles the workload effortlessly and with exceptional efficiency. Renowned for its low energy consumption and minimal CO₂ footprint, the KAESER Aircenter not only supports sustainability goals but also delivers reliable, round-the-clock performance tailored to meet the needs of modern dental laboratories.
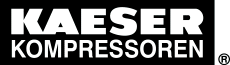
Carl-Kaeser-Str. 26
96450 Coburg
Germany
96450 Coburg
Germany
Hall 10.1 | F069